Heimsheim. 3D-printing is everywhere. How far additive manufacturing can go this is shown in the project DIMAP. As outstanding outcome of the H2020 project DIMAP, cirp will showcase the first ever pneumatic robot in the world printed almost exclusively with PolyJetTM technology from Stratasys® at the exhibition formnext 2018.
DIMAP, standing for “Novel nanoparticle enhanced Digital Material for 3D Printing and their application shown for robotic and electronic industry”, is a multidisciplinary research project focusing on the development of novel 3D-printing materials for PolyJetTM technology.
A group of 12 partners from five different countries coordinated by PROFACTOR developed ink materials with special thermal and electrical conductive properties within the scope of the project
Due to its qualities, these ink materials can be used for selected print heads as well as be tailored to suit future industrial applications in products.
The DIMAP SCARA robot displays impressively the potential of the PolyJetTM 3D-printing technology with new developed ink materials. The robot will be presented to the public for the first time this November at the formnext exhibition. SCARA is the abbreviation for Selective Compliance Assembly Robot Arm and describes a jointed-arm robot that can operate horizontally. DIMAP stands for Novel nanoparticle enhanced Digital Materials for 3D Printing and their application shown for the robotic and electronic industry. From 2015 to 2018, Profactor has coordinated a group of 12 partners from five different countries focused on the development of novel materials for PolyJetTM printing technology. The European Union has funded this joint project within the framework of the program Horizon 2020.
PolyJetTM is a 3D-printing technique where print heads jet layers of curable liquid photopolymer materials, so called inks, onto a build tray. So layer by layer complex models get shaped. Multiple inks can be printed simultaneously in one layer to combine different characteristics or colors in one printed object. DIMAP aimed to develop ink materials with an innovative set of properties:
- Electrical conductive ink with silver nanoparticles to print conductive tracks
- Thermal conductive ink with ceramic nanoparticles to cool LED lights
- Foamed ink for light-weight applications
- Polyimide inks with excellent chemical and high temperature resistance.
A prototype PolyJetTM printer with extended processing features was created within the project to allow the printing process with the novel ink materials.
Two demonstrators were developed to test the printing suitability of the new ink formulations: a customizable luminaire and a pneumatically operated robot. Festo, a German supplier of pneumatic and electrical automation technology, was responsible for the design and startup of the DIMAP SCARA, which is a pneumatically actuated robot. Its functional plastic components have been printed with PolyJetTM additive manufacturing technology. Two movable axes display two different solutions for a printed rotary drive. Altair’s simulation software was used to optimize further structural components, such as the lightweight gripper. Additive manufacturing enabled a high functional integration with a small amount of components and a particularly light structure.
Gabriel Dämmer, Project official at Festo says: “Regardless if Additive Manufacturing is considered for prototyping or for the manufacturing of end-use products, understanding and incorporating the technological capabilities into specific design processes is essential. The development of the DIMAP SCARA gives us first hand experiences of Multi-Material Additive Manufacturing in the field of pneumatic light-weight robots.”
The German company cirp manufactured the plastic components of the robot with a modified Stratasys’ Objet260 Connex2TM printer using the newly developed inks supplied by the different partners as well as standard materials from Stratasys.
cirp will show the unique DIMAP robot in action at its exhibition stand at the formnext (hall 3.1 booth F11 + G10).
Leo Schranzhofer, project leader of DIMAP says: “DIMAP gives us a glimpse into future possibilities of PolyJetTM printing, nicely shown with the DIMAP SCARA robot, developed by FESTO and printed by cirp. The outcome of DIMAP opens the door to a new generation of highly functional products”.
cirp: The company, based in Heimsheim near Stuttgart, has been manufacturing plastic parts as prototypes and small series for a wide variety of industries with additive manufacturing and injection moulding since 1994. The processes at cirp include PolyJetTM, stereolithography, laser sintering, FDM, vacuum casting, CNC milling.
Booth number at formnext: Hall 3.1 Booth F11 + G10
Festo AG is a global player and an independent family-owned company with headquarters in Esslingen am Neckar, Germany. The company supplies pneumatic and electrical automation technology to 300,000 customers of factory and process automation in over 35 industries. The products and services are available in 176 countries. With about 20,100 employees in over 250 branch offices in 61 countries worldwide, Festo achieved a turnover of around €3.1 billion in 2017. Each year around 8 % of this turnover is invested in research and development. In this learning company, 1.5 % of turnover is invested in basic and further training. Yet training services are not only provided for Festo’s own staff – Festo Didactic SE also supplies basic and further training programmes in the field of automation technology for customers, students and trainees.
PROFACTOR: is an Austrian research company located in Steyr and focuses on developing new methods for integrated production technologies. The technological focus is on robotics, machine vision, functional surface and nanostructures. About 75 scientists of various disciplines conduct research to improve the competitiveness of the production industry and to strengthen the Austrian and European industry. PROFACTOR strives to enhance printing technologies that create solutions for functionalizing surfaces. This is the key to innovative and individual products with outstanding properties.
Stratasys is a global leader in additive manufacturing or 3D printing technology, and is the manufacturer of FDM® and PolyJet™ 3D Printers. The company’s technologies are used to create prototypes, manufacturing tools, and production parts for industries, including aerospace, automotive, healthcare, consumer products and education. For 30 years, Stratasys products have helped manufacturers reduce product-development time, cost, and time-to-market, as well as reduce or eliminate tooling costs and improve product quality. The Stratasys 3D printing ecosystem of solutions and expertise includes: 3D printers, materials, software, expert services, and on-demand parts production. Online at: www.stratasys.com, http://blog.stratasys.com and LinkedIn.
Stratasys is a registered trademark and the Stratasys signet is a trademark of Stratasys Ltd. and/or its subsidiaries or affiliates. All other trademarks are the property of their respective owners.
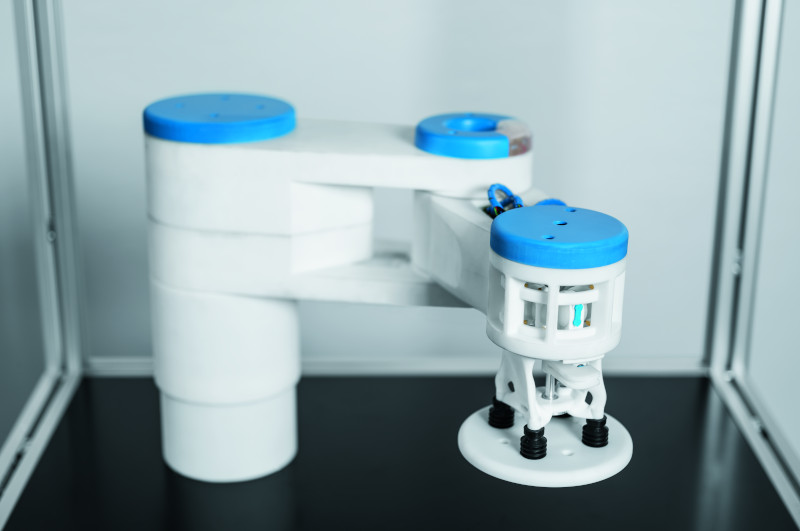
3D-printed robot DIMAP SCARA shows the potential of PolyJetTM technology
Picture: © FESTO